Nate • 13 May 2025
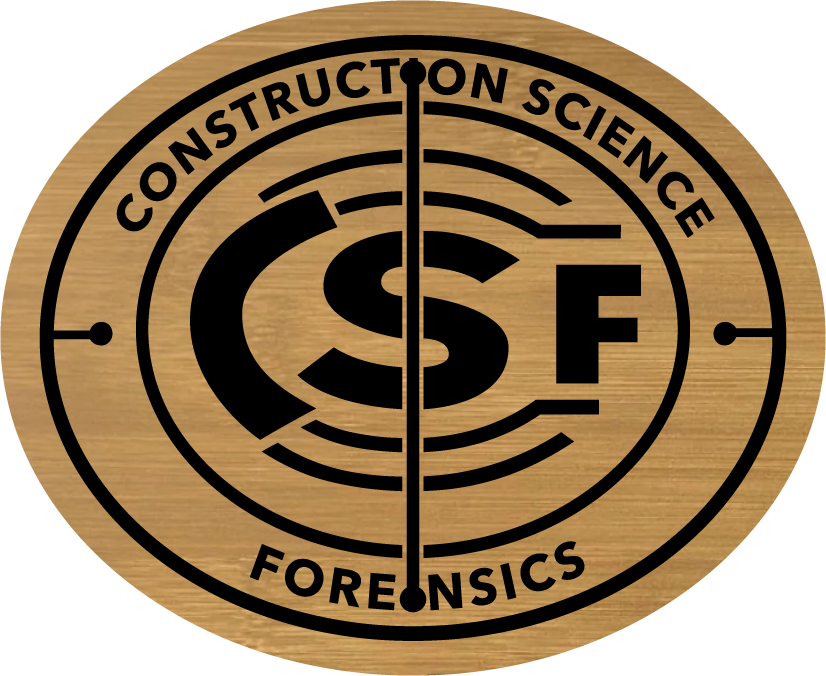
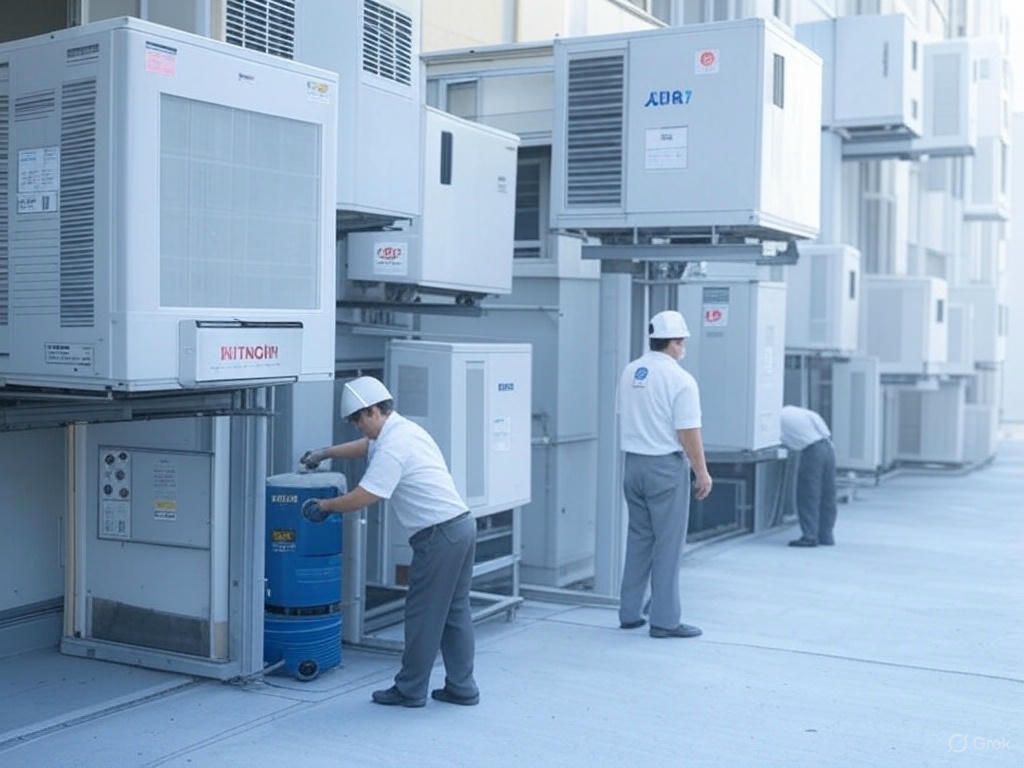
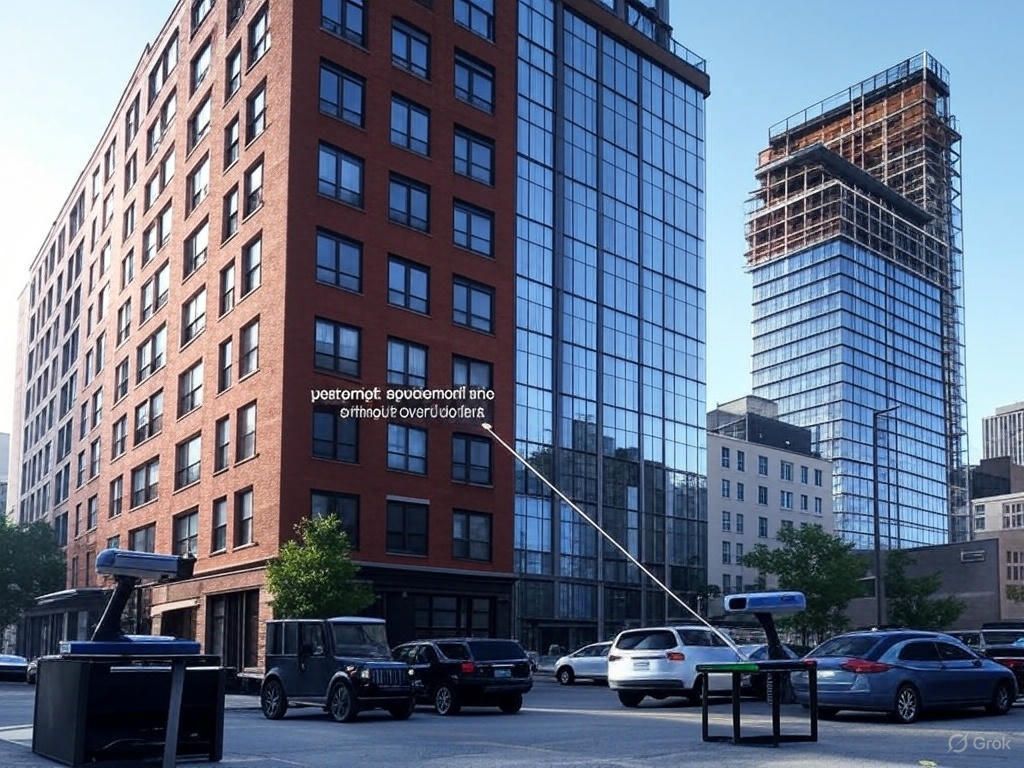
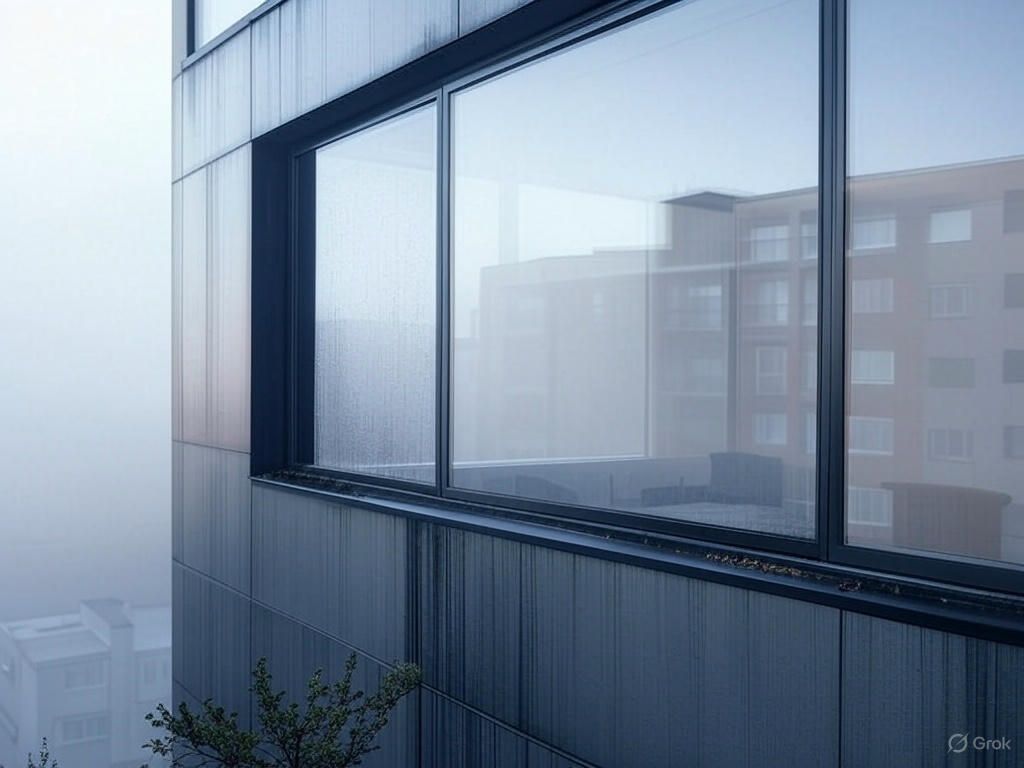
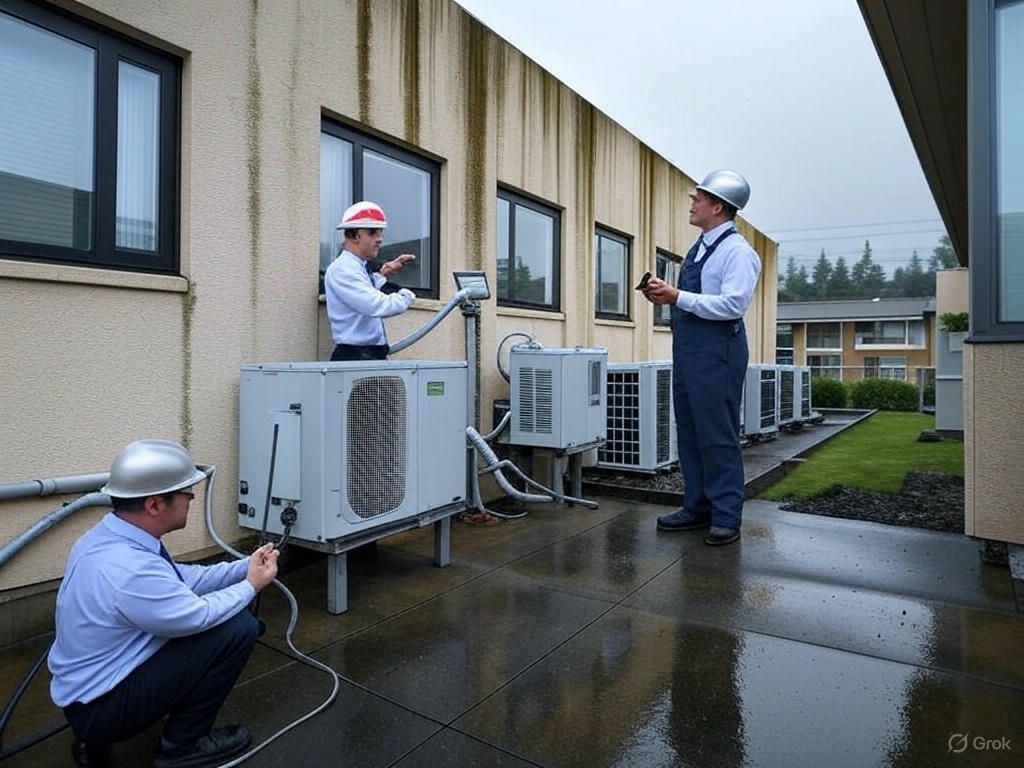
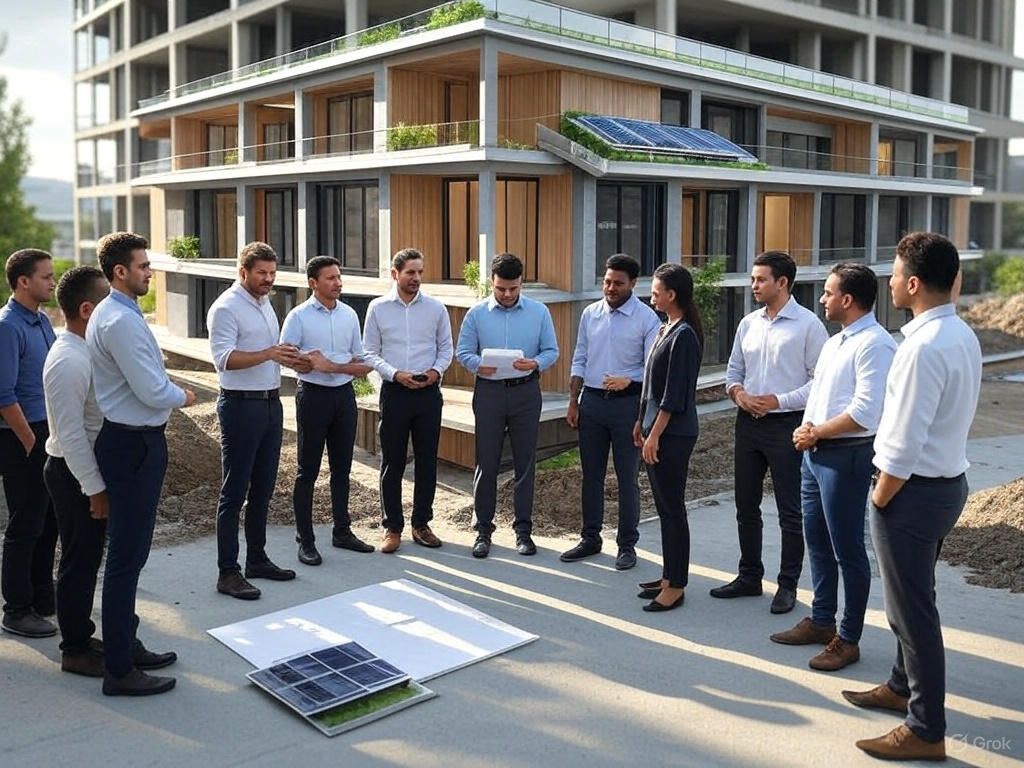
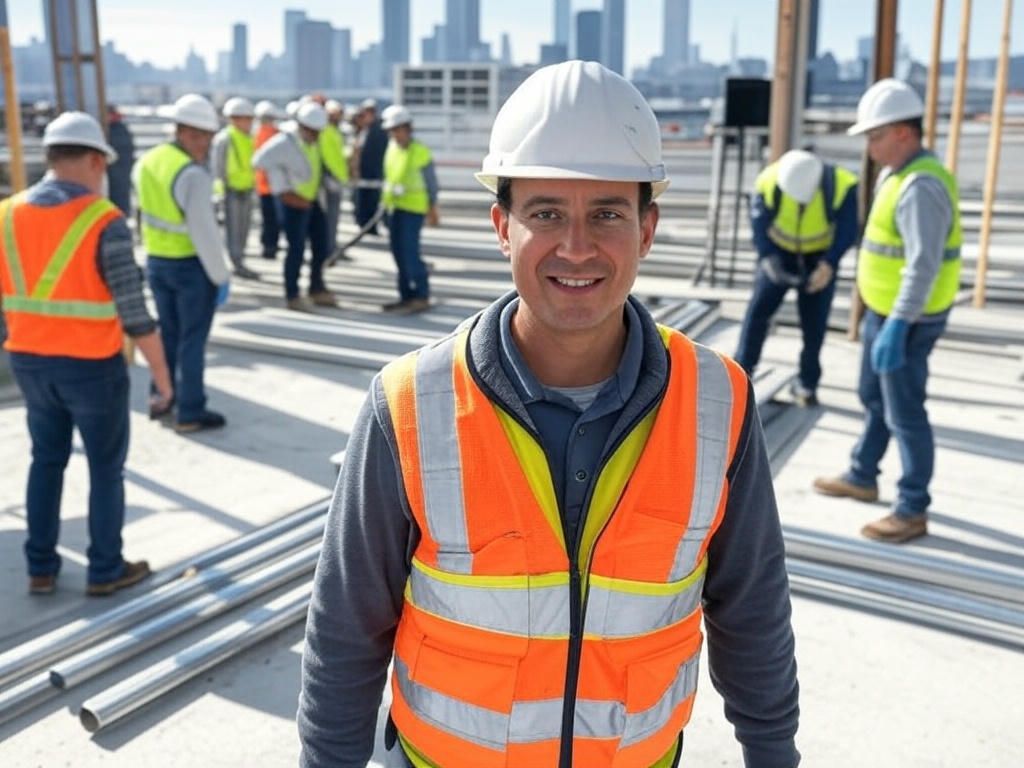
The Ultimate Guide to becoming a Top-tier Construction Expert/Consultant
"The Ultimate Guide to becoming a Top-tier Construction Expert/Consultant" by Nate MacIntyre. It is a guide to mastering the construction and construction law industry, providing insights into construction standards and legalities that govern the industry. The book is based on the author's two decades of experience in the field and is intended to serve as a reference guide for understanding the construction expert/consulting industry. The book is divided into several chapters, including "Laying the Foundation," "Building Experience," "Advanced Credentials," "Professional Networking," and "Strategic Career Moves." Each chapter provides valuable information and advice for those aspiring to reach the top echelons of construction expertise.
For Purchase on Amazon: https://a.co/d/izCoCnF
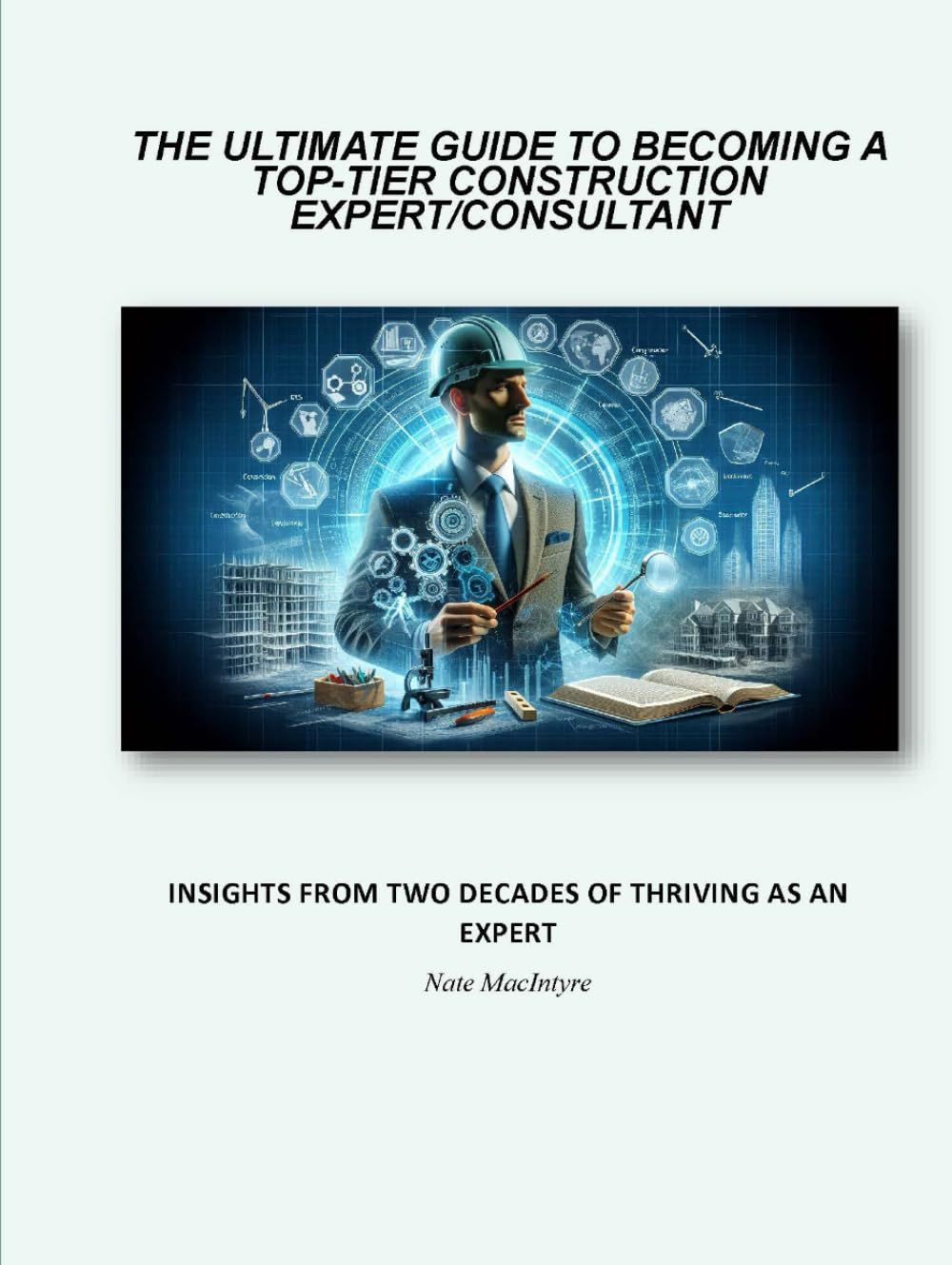
Residential Construction: A Guide for Anyone who Needs to Understand the Construction of a Single-Family Home
The purpose and scope of the book: The book is intended to serve as a reference guide for understanding the construction of a single-family home, covering various components, systems, and roles involved.
The forces that a residential structure must withstand: The book explores the different natural and human-made forces that affect the stability and safety of a house, such as dead and live loads, environmental forces, seismic forces, thermal forces, soil and foundation forces, hydrostatic forces, and fire resistance.
The symphony of construction: The book uses the metaphor of a symphony to describe the intricate collaboration of various elements and expertise that culminate in the creation of a home. It provides an overview of the main components and systems, such as foundation, framing, mechanical, electrical, plumbing, roof, exterior, and site.
The orchestra of professionals: The book also introduces the diverse group of professionals that orchestrate the construction process, from land acquisition and feasibility experts, developers, architects, engineers, municipal authorities, contracting teams, to skilled tradespeople. It highlights their collective expertise and contributions to the project’s success.
The communication and collaboration challenges: The book acknowledges the challenges and pitfalls that can arise from poor communication and collaboration among the various stakeholders involved in construction projects. It offers tips and strategies to ensure clear and productive interactions, such as defining project expectations, maintaining regular and open communication, using visual aids and documentation, being open to questions and concerns, and seeking professional assistance when needed.
The role of technology and innovation: The book showcases the role of technology and innovation in enhancing communication and collaboration in the construction industry. It presents examples of tools and technologies that transform construction processes, such as mobile applications, virtual and augmented reality, cloud-based collaboration platforms, building information modeling, and construction robots. It also provides case studies of innovative solutions that address complex challenges and improve the efficiency, safety, and sustainability of construction.
For Purchase on Amazon: https://a.co/d/9eZe68v
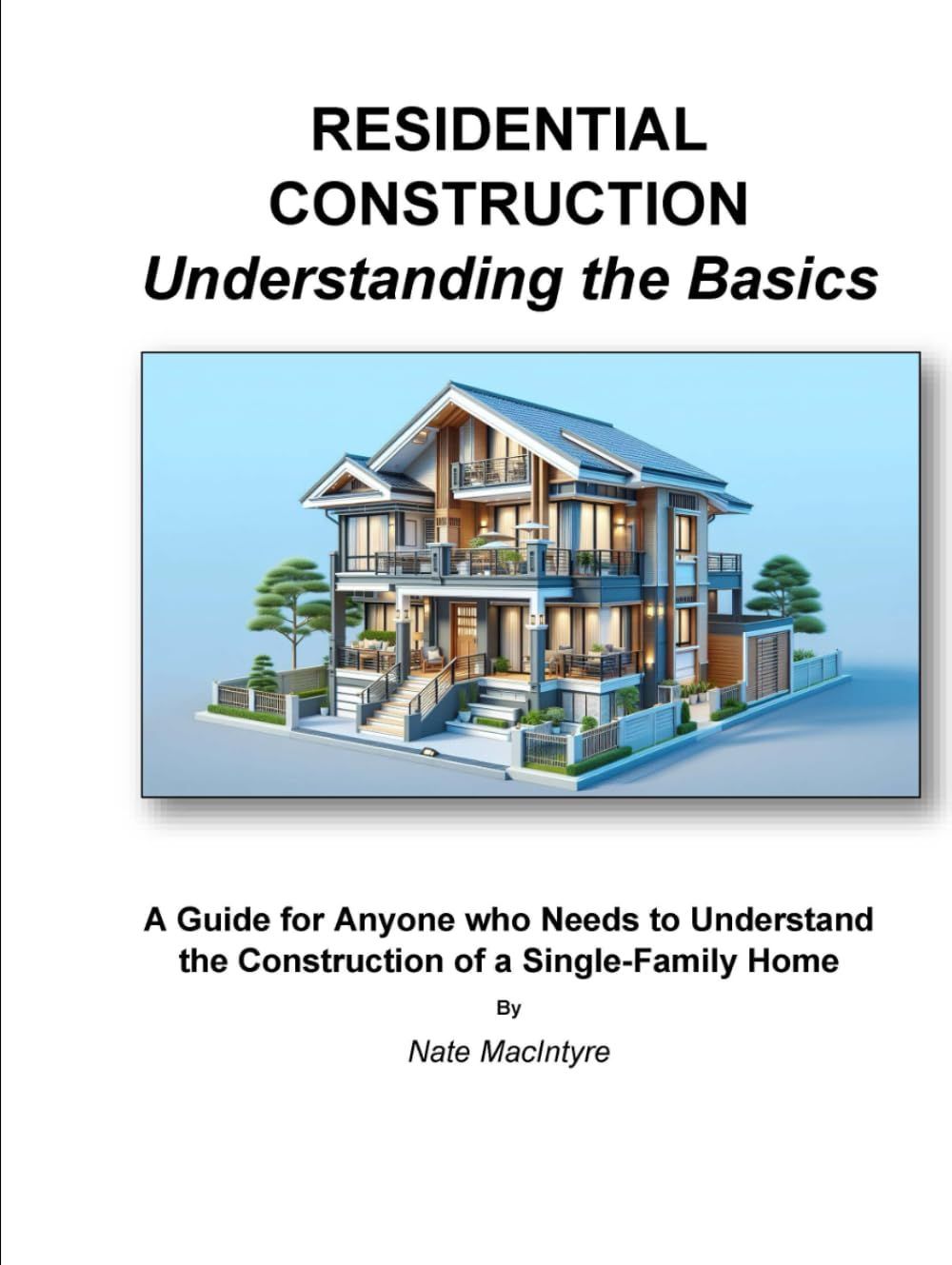
Wetting and Drying of Wood Structures During Construction
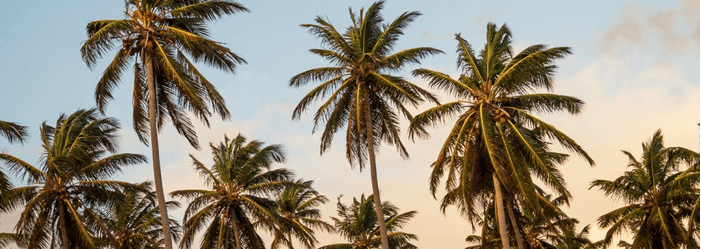
Construction involves a myriad of materials, each with its unique properties. One such material is wood, which is often subjected to wetting and drying cycles during construction. This blog post will delve into the intricacies of these processes, discussing adsorption, absorption, and desorption rates for different materials, moisture content requirements for various construction materials, and code requirements for drying materials prior to covering.
Wetting and Drying of Wood Structures
Wood structures are often exposed to moisture during construction, leading to wetting and drying cycles. Wetting occurs when wood absorbs water, while drying happens when the absorbed water evaporates. The rate at which these processes occur depends on several factors, including the type of wood, environmental conditions, and the moisture content of the wood.
Adsorption, Absorption, and Desorption
Adsorption refers to the process where atoms, ions, or molecules from a gas, liquid, or dissolved solid adhere to a surface. In contrast, absorption involves mass transfer into another material. Desorption, on the other hand, is the reverse of adsorption and absorption, where the adsorbed or absorbed substance is released. The rates of these processes depend on factors like temperature, pressure, and the nature of the adsorbent and adsorbate.
Moisture Content Requirements for Construction Materials
Different construction materials have specific moisture content requirements to ensure their optimal performance and longevity. Here are some general guidelines:
· Concrete: Concrete should be allowed to cure properly and reach a stable moisture content before any covering materials are applied. The specific moisture content can vary depending on the type of concrete and its application.
· Insulation: Insulation materials should be kept dry during installation to maintain their thermal resistance properties.
· Drywall: The ideal moisture content for drywall ranges from 5% to 12%.
· Plywood and OSB: Wood-based sheathings like plywood and OSB should have a moisture content of 19% or less.
· Gyp Sheathing and Gypcrete: Exterior gypsum sheathing should have a moisture content of 1% or less. For gypcrete, a moisture content threshold of 1% or less is considered conservative, although some manufacturers recommend 5% as the threshold.
Code Requirements for Drying Materials Prior to Cover
Building codes often stipulate requirements for drying materials before they are covered to prevent potential issues such as staining, mold, excessive dimensional changes, and decay. For instance, materials showing visible signs of water damage or mold should not be installed. All building materials should be stored in a dry location and inspected prior to installation.
Understanding the wetting and drying processes of wood structures during construction is crucial for ensuring the durability and longevity of the built structure. By adhering to the moisture content requirements for different materials and following the code requirements for drying materials prior to cover, construction professionals can mitigate potential moisture-related issues and enhance the performance of the building materials.
Remember, the specifics can vary based on local building codes and manufacturer recommendations, so always check these sources when planning your construction project.
Preventing mold growth during construction is crucial to ensure the longevity and safety of the structure. Here are some strategies you can employ:
1. Proper Site Preparation and Drainage: Effective mold prevention starts with proper site preparation and drainage. This helps to prevent water accumulation, which can lead to mold growth.
2. Controlling Moisture and Humidity Levels: It's important to control moisture and humidity levels during construction. This can be achieved by using dehumidifiers and ensuring proper ventilation.
3. Adequate Ventilation and Airflow: Proper ventilation and airflow can help to control humidity levels and prevent the accumulation of moisture.
4. Using Mold-Resistant Materials: opt for mold-resistant materials such as certain types of drywall and insulation.
5. Regular Inspections and Maintenance: Regularly inspect the construction site and materials for signs of mold growth. If mold is detected, it should be addressed immediately to prevent further spread.
6. Dry the Building In: Seal the building envelope so that no water can get through. This can be achieved by installing a water-tight roof, using water-tight exterior siding on the house, installing water-tight windows, and sealing every opening around the windows, doors, and other areas.
7. Dry the Materials Out: Give materials time to dry out after they get wet in the rain or snow. For example, wooden frames and subfloors tend to hold moisture after a weather event and then release it indoors while you’re drying the building in.
8. Eliminate or Tend to New Humidity Sources: Sometimes, even drying-in isn’t enough to get rid of moisture and the mold can continue to grow. That usually happens when you introduce a new source of moisture to the house. One way address this new source of moisture is to wait for it to evaporate and then continue construction. But if you’re on a tight schedule, you might want to use some dehumidifiers during the renovation.
Drying wet wood framing and sheathing prior to covering is crucial in construction to prevent issues such as mold growth, structural instability, and material degradation. Here are some of the best methods for drying wet wood framing and sheathing:
1. Time: Given enough time, and assuming the wood isn't getting wet again, the wet lumber will naturally dry. If the outdoor temperatures are above 60 degrees F, it won't take much time, maybe 3-5 weeks to get from 18% down to 14%. However, if it's cold and rainy outside, it might take 6-12 weeks. If it's below 32 degrees F, it will take a long time to dry.
2. Air Movement: This is the first and easiest tool in the drying toolbox. Using fans to blow on the wet areas of the house can help speed up the drying process. If the weather is above 45 degrees F during the day, then a fan blowing on a wet area of framing will dry down about 0.5-1% per day.
3. Dehumidification: Controlling the humidity is key to really drying down your framing. If the air outside is above 60% humidity, it's recommended to shut down your windows/doors and run your fans in combination with a dehumidifier.
4. Heat: Applying heat can also help to speed up the drying process. However, this method should be used with caution as excessive heat can cause the wood to warp or crack. Also, ensure your heat source will not add moisture to the indoor environment.
Measuring the moisture content of wood is crucial in many applications, including construction and woodworking. Here are some methods you can use:
1. Using a Moisture Meter: This is the quickest and most common method. There are two types of moisture meters: pin-type and pinless.
· Pin-Type Meters: These meters have two measuring tips that you need to slightly prick into the wood to get the moisture percentage. The device uses electric current to determine the resistance of the wood. The higher the resistance, the drier the wood.
· Pinless Meters: These meters can be useful if you need to detect moisture in a non-destructive way. They are somewhat easier to operate than pin meters, however, they are usually less precise and cost more. Most pinless meters should be calibrated for the thickness and type of wood.
2. Oven-Dry Testing: This is a more scientific method. The moisture content (MC) is the measure of how much water a piece of wood contains compared to its oven-dry weight. Oven-dry weight is determined by heating the sample at a temperature over 100º C until its weight does not change anymore, which indicates that all water has been expelled from the sample.
3. Non-Destructive Testing: These methods do not require damage or destruction to the material being tested. The two common non-destructive methods are the electrical resistance method and the electrical conduction method.
· Electrical Resistance Method: This method measures the electrical resistance between two electrodes placed in contact with each other when passed through a sample of wood. The electrical resistance changes according to fluctuations in MC and provides an accurate result quickly with minimal disturbance to the material being tested.
· Electrical Conduction Method: This method works by passing a low voltage alternating current between two closely placed electrodes on either side of a sample piece while mounted in a cup measuring vessel with an electrolyte solution.
Remember, the specifics can vary based on the type of wood and the specific moisture meter model, so always check the manufacturer's instructions when using these tools.
There are several industry association standards that provide guidance on where and when to test moisture content in wood framing and wood sheathing during construction. Here are some of them:
1. American Wood Council's Wood Frame Construction Manual (WFCM): The WFCM provides guidance on the design and construction of wood-frame buildings. While it doesn't specify moisture content testing procedures, it does provide general guidelines on wood framing and sheathing practices that can help prevent moisture-related issues.
2. Bessemeter's Guidelines: Bessemeter, a company specializing in moisture issues, suggests that the industry standard for acceptable moisture content (MC) in wood framing varies depending on the location, typically between 9% and 14% MC. They recommend using a quality moisture meter to take readings and show them to homeowners as a precaution.
3. Wagner Meters' Guidelines: Wagner Meters provides a comprehensive guide on acceptable moisture levels in wood from diverse perspectives, including builders. They recommend using a moisture meter to accurately measure these levels.
4. Use good judgement. Assess the structure as a whole system when conducting moisture testing. Ensure large wood framing members that are covered with wood sheathing are measured for adequate dryness prior to covering.